Fiberglass
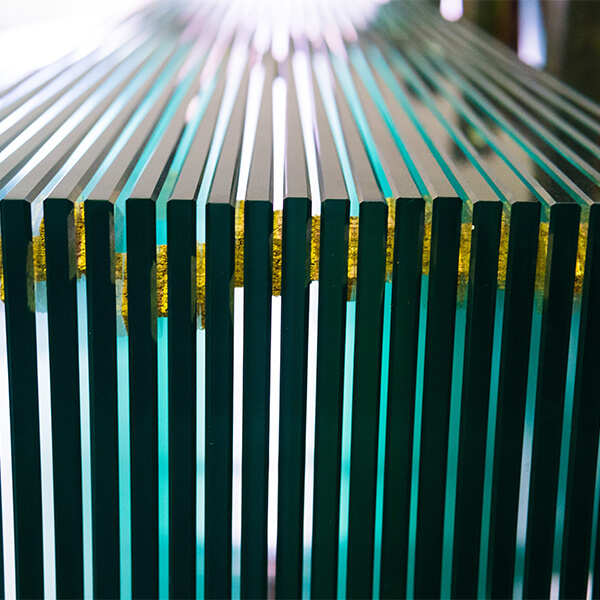
Elevating Performance with Tailored Fiberglass and Kaolin Solutions
Hydrous kaolin and calcined kaolin play essential roles in fiberglass manufacturing, each contributing unique benefits to the process and final product.
It reduces resin consumption while improving the bulk and aesthetic quality of the product, making it ideal for general-purpose fiberglass applications such as insulation, automotive parts, and construction materials. On the other hand, calcined kaolin, which undergoes high-temperature treatment, is tailored for high-performance fiberglass applications requiring superior strength, durability, and heat resistance.
Hydrous Kaolin in Fiberglass
Applications
- Filler and extender in general-purpose fiberglass.
Key Benefits
- Mechanical Properties: Improves strength, stiffness, and bulk.
- Cost Efficiency: Reduces resin consumption, lowering production costs.
- Surface Quality: Enhances smoothness, opacity, and brightness.
- Durability: Offers moderate weather and chemical resistance.
- Processing Aid: Improves resin flow and serves as a thickening agent.
Common Uses
- Insulation, automotive parts, construction materials, pipes, tanks, and other low-cost fiberglass products.
Calcined Kaolin in Fiberglass
Applications
- High-performance filler and reinforcing agent.
Key Benefits
- Mechanical Properties: Provides superior strength, rigidity, and durability.
- High Heat Resistance: Ideal for fireproofing and high-temperature uses.
- Surface Finish: Enhances smoothness and durability.
- Fire Resistance: Excellent flame-retardant properties.
- Cost Efficiency: Reduces resin usage in premium applications.
Common Uses
- Aerospace, automotive, fire-resistant panels, marine applications, and high-strength sports equipment.
Conclusion
- Hydrous Kaolin: Cost-effective for general fiberglass products with reasonable performance.
- Calcined Kaolin: Ideal for high-performance applications requiring strength, heat resistance, and durability.